Use Case: Intermediate Bulk Container Level Monitoring
The complexity of monitoring 681M intermediate bulk containers
Accurately measuring the contents of intermediate bulk containers is of key importance.
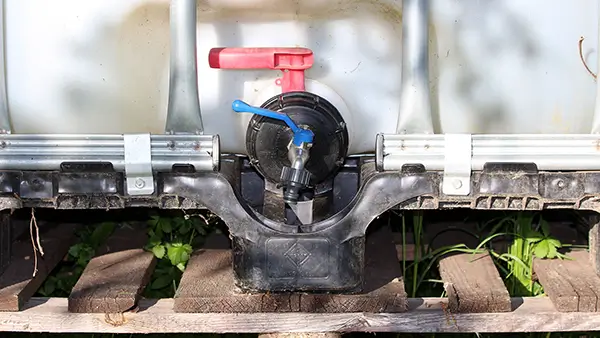
Rigid intermediate bulk containers (IBCs) are essential in today’s manufacturing industries. They are responsible for storing and allowing the transportation of a wide diversity of industrial materials such as water, chemicals, oils, pharmaceutical compounds, and liquid foodstuffs. Because of this versatility, they are widely adopted in a multitude of critical industries where IBCs can be used in their hundreds with each having an average capacity of 1,000 liters. It is therefore essential for operatives to monitor the level of these stored containers to check proper usage rates and maintain adequate stock levels.
Most current liquid level sensing solutions require inconvenient installations with mechanical gauges or submerging rods inside a container which is not scalable nor is compatible with some liquids. Newer non-contact ultrasonic and radar sensors are easier to install, however, they rely on a signal that may lose reliability due to condensation, foam or long measuring distances. An easy-to-install, scalable, and non-contact level sensor is required for efficient IBC monitoring.
Market opportunity for IBC
-
There are 681M IBC units in circulation globally.
-
The IBC market was valued at US$21B in 2021, and is predicted to grow by US$3.18B during 2021-2025, progressing at a CAGR of 6.45%.
-
IBCs and rigid plastic packaging are the two fastest-growing segments within the industrial packaging market.
-
The chemicals industry, which is the dominant segment for IBC demand, is predicted to grow to US$4.3T by 2025 at a CAGR of 4%.
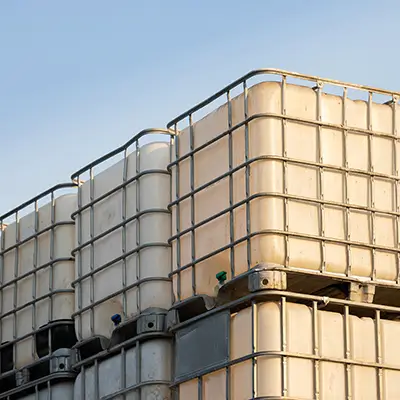
IBC market dynamics
The strong growth in the IBC market can be attributed to the increase in containerization which is fueled by the advance in global manufacturing. As IBCs can be used for a range of liquids and bulk materials, strong demand is present in many industries such as chemicals, food and beverages, healthcare, and construction. This is leading to a range of standardized IBC containers such as UN-rated or food-safe variations to cater for specific use cases.
Global trade is also increasing demand for cost-effective transportation solutions that allow IBCs to show their superiority over other packaging types. IBCs are mostly made from HDPE, which makes their production very economical and performs well structurally. Rectangular IBCs are also more space-efficient and transportable than drum containers, which amounts to an impressive 75% decrease in overall costs.
IBC usage is widespread globally, but is particularly concentrated in China due to it having the world’s largest chemical market. Rapid industrialization and manufacturing activities in the Asia Pacific region are also driving the market for plastic IBCs.
A factor that may harm IBC use is that raw materials such as HDPE pellets have volatile prices, meaning container prices can rise unexpectedly. While this impacts their production, IBCs are highly reusable, so they can be reconditioned to extend their use. It is also reported that IBC vendors are investing more in production capabilities and reconditioning - for example Mauser Packaging Solutions, who are a global leading supplier, are buying more advanced equipment for these reasons.
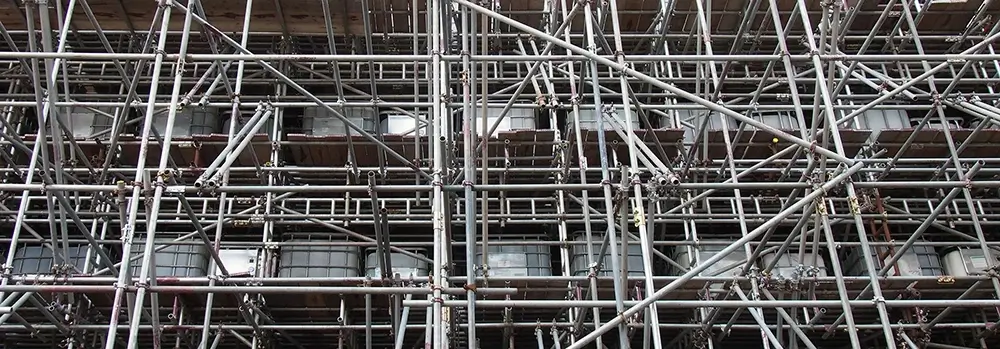
Manually monitoring IBCs at an industrial scale is not feasible
IBCs can be used in large-scale setups whether in warehouses or construction sites where they can be moved quickly with just a pallet truck. While taking stock levels manually for a few containers may be manageable, this would be very inefficient at the industrial scale. Manual inspection is tedious and if not frequent enough, could lead to running out of stock- or the opposite with overfilling tanks. Furthermore, checking the operational flow rate for more than one IBC becomes very time-consuming. Therefore automatic level checking is necessary for efficient IBC usage and maintenance.
This is especially important for time-sensitive fluids such as water because water contained for more than six months can become toxic and not suitable for consumption. Not having this data can make it very difficult for factory workers to maintain efficient production.
Additionally, high volumes of stored liquids create a potential for accidents such as leaks, which not only can be a hazard for workers but can create further environmental issues. For example, toxic chemicals escaping into surrounding water sources. Flammable liquids also need close monitoring as once leaked, this can pose serious fire hazards in an already high-risk area. These dangers mean that automatic monitoring of a container’s level is essential for proactive production lines and preventing accidents.
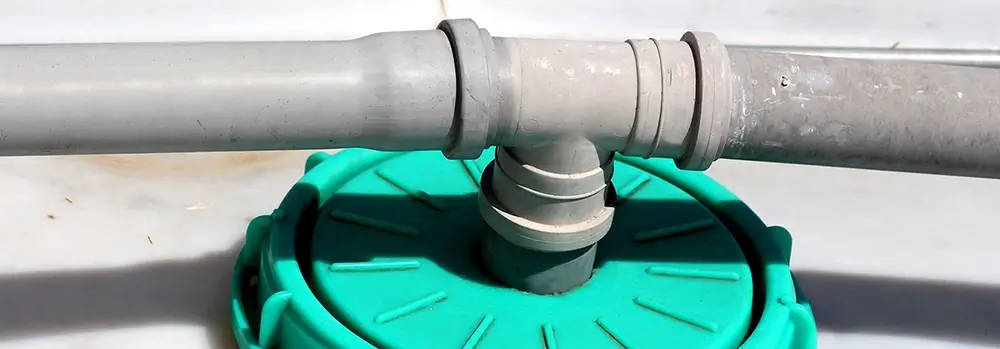
Competitors
IoT level sensors have been employed for a range of IBC applications, whether triggering alarms for empty IBCs or measuring their exact level. These level sensing mechanisms offer a range of accuracies, and can be categorized whether float, weight, optical, differential pressure, capacitance, conductive, ultrasonic or radar. Regardless of the accuracy, companies that manage a large IBC network need a scalable sensing system in terms of both cost and installation as well.
Load cells and contact solutions
IBC weighing systems or load cells are very accurate and require minimal installation, but are costly and cannot monitor stacked IBCs as separate units. Float gauges operate using a float placed in the liquid that moves with the water level. This float can either be attached to a pulley where the other end points to a visual gauge to read the current level, or the float triggers external switches to notify whether the container is empty or full . These float systems can require many mechanical elements that require modifying a container’s existing structure, making them difficult to scale installation-wise. This is not to mention the unreliability of the float which can get tangled or damaged by the liquid contents.
Capacitance-based sensors reduce the need for moving parts, as they have probes installed that are in contact with the liquid that measure the change in capacitance with reference to air. However, as they are still in contact with the liquid contents, this may not be an option for corrosive liquids or liquids that cannot be contaminated.
Non-contact solutions
Ideally, non-contact solutions would overcome installation difficulties and be adaptable to a range of containers regardless of the liquid. Non-contact capacitive sensors use the same capacitive sensing mechanism, but can be placed on the outside of non-metal containers. These are mostly only available as discrete switches that do not provide a continuous reading of the whole tank height.
Ultrasonic and radar sensors, on the other hand, are non-contact and can also measure exact levels of a liquid on a continuous scale. Ultrasonic level devices are installed at the top of a container and emit sound waves to locate the liquid's surface. Unfortunately, ultrasonic sensor readings can be skewed by irregularities within the container such as foam, condensation and vaporous media. Radar sensors overcome these disruptions by using much higher frequencies via microwave pulses to provide more accurate readings.
However, despite these non-contact devices, their accuracy can attenuate when the liquid is furthest away from the sensor. They also come with a hefty price tag, so may not be economically feasible for factories with many IBCs. Therefore IBC level monitoring needs a cost-effective, easy-to-install solution capable of accurate readings along the whole height of the container.
LAIIER's solution for IBCs: A non-contact, easy to install sensor
To address these shortcomings, LAIIER has developed a non-contact level sensor that can be applied like a sticker to the outer surface of an IBC. Due to the innovative, flexible sensor design, the sensor can be manufactured to any desired length to accurately measure the full extent of the container. Additionally, all of LAIIER’s sensors are connected to our Surface to Cloud™ platform via LoRaWAN technology so devices can promptly notify facility managers of any issues and actions required.
As IBCs can be regularly moved around in an industrial warehouse, level monitoring can be disconnected and IBCs lost track of. However with LAIIER’s system, monitoring will not be disrupted as firstly, the thin sensing devices do not need to be removed whilst the container is being moved. And more importantly, as long as there is an internet connection, the container’s level will always be communicated via LoRaWAN. LAIIER’s sensing devices can therefore be easily and economically scaled to cater to however many IBCs are needed in one facility.
Market demand for IBC
IBC vendors
The IBC market is highly competitive with a strong presence of both local and global companies such as Mondi Group, Mauser, and Grief Packaging. To maintain a competitive edge, these companies offer a range of IBC specifications where dispensing valves, chemical compatibility and level sensing can be a key selling point. Therefore by incorporating a streamlined level-sensing system into IBC products, this can add the much-needed value for the ever-growing manufacturing industry.
Facilities/ operations managers
Level monitoring of IBCs can provide a wide range of actionable insights for facility managers, especially for factories that manage a large network of IBC containers. Knowing exactly how much of a liquid has been transferred and its flow rate is sometimes integral in order to meet legal or commercial requirements. Furthermore, from an operations standpoint, making sure all IBCs are filled sufficiently will prevent hold-ups in the production line from empty IBCs and can notify when more items need to be procured. Level-sensing can also infer any abnormal activity such as leaking, potentially preventing serious accidents.
Commercial insurance providers
As mentioned, IBCs can contain toxic or flammable chemicals that can lead to costly accidents such as those related to a production worker’s health, fire incidents or environmental pollution. IBCs are designed to be transported to many stages of a production line so present a potential danger in a range of settings if damaged. Tampering and theft are also possible when the contents are highly valuable. These incidents can lead to large payouts by commercial insurance providers who are not aware of these risks. Therefore insurers can provide customers with level monitoring systems that can prepare a degree of security and allow for early actions.
IBCs, as one of the most efficient and economical methods of containing liquids and bulk solids, will be an integral component of future stock management and production lines. Whilst this is the case, monitoring IBC levels are limited to mechanical solutions or expensive devices that may not be scalable for factories processing hundreds of IBCs. LAIIER has provided an easy-to-install, cost-effective sensor that can span the height of an IBC to accurately communicate current liquid levels and flow rates to facility managers. Via the sensor's Surface to Cloud™ platform, stakeholders can be alerted remotely of any issues so actions can be taken effectively.