Use Case: Oil Filled Transformer Leaks
10,000 gallons of danger
Early detection of small oil leaks from electrical transformers in substations.
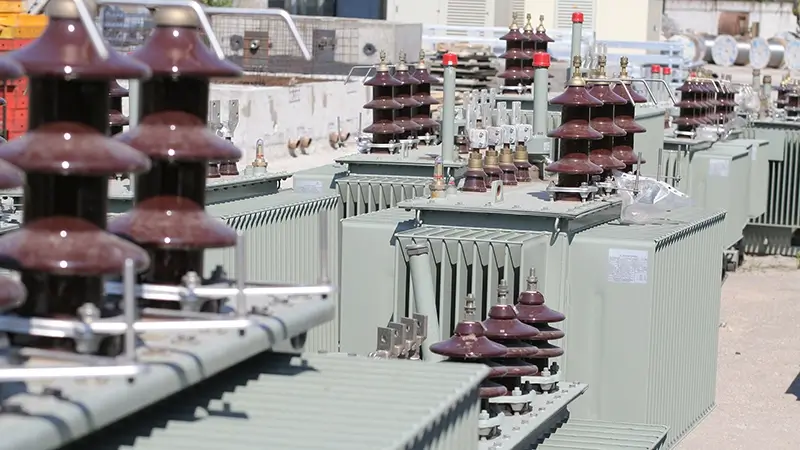
Electrical transformers are an integral part of every nation's power distribution infrastructure. Without them, transferring electricity from power stations to towns and cities would be impossible. Controlling very high levels of current and voltage from power stations to local networks releases a lot of heat that must be safely dissipated. Oil-immersed transformers are the most effective cooling mechanism and typically contain a staggering amount of 10,000 gallons of oil. This huge volume of oil combined with the already hostile environment of high temperatures, high voltages and the outdoor weather can leave transformers prone to serious damage if left uninspected.
Damage can start from small oil leaks around gaskets, flanges and radiator fins which can escalate to rupture tanks and create major fire incidents. Whilst repairs can be costly, the secondary impacts of worker injuries, environmental pollution, and power downtime can easily out shadow initial costs. Despite the severity of the damage, most methods of transformer inspection are done manually on a reactive basis- patching up leaks where seen. This can miss hidden parts of the complex transformer design. An easy-to-install, wide covering and accurate sensing solution is needed to detect the first drops of oil transformer leaks.
Market opportunity for power transformers
- The global market for power industry transformers exceeded US$45B in 2021 and is predicted to reach US$93B by 2030 (CAGR of 7.1%).
- In the US alone, there are 55,000 transmission substations, each containing around 1 to 4 transformers.
- For the highest voltage category of transformers (345 kV and above), there are around 2,100 of these transformers in the US.
- The global transformer oil market is valued at US$1.9B in 2021 and is projected to reach US$3.3B by 2030 (CAGR of 6.5%).
- The leak detection market for oil and gas is projected to reach US$3B by 2025 with a CAGR from 2020 of 7.8%.
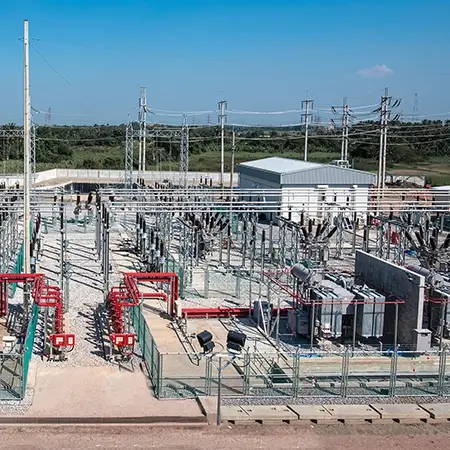
Power transformer market dynamics
Global energy consumption is forecast to rise by 39% by 2030, and as demand increases, more infrastructure investment is required from energy distributors. This ultimately means more and better quality substations and transformers are needed. Regardless of whether energy is renewable or not, transformers will still be a ubiquitous part of the grid. And as renewable energy consumption increases, these sources tend to be located in further, more remote regions so arguably more robust transformers will be required to bridge this distribution.
In addition to higher demand, more cross-national electricity systems mean upscaling transformer infrastructure. For example, the European Union (EU) is planning a pan-European grid to connect multiple countries as well as the Indian Energy exchange who propose a South Asian regional power market integrating 5 neighboring countries. This is expected to increase transformer demand and their performance.
Due to the vast quantity of up to 30,000 gallons of oil, regulators are aware of the potential dangers of poor maintenance and thus detail tighter standards for transformers in substations as seen in OSHA (US) and EU directives. More generally, oil pipes in some states will soon be mandatory to be cable protected and unprotected facilities will be penalized heavily. This could be transferable to oil leak risks in substations, given their scale.
In the transformer market, there are two types of transformers: oil-immersed and dry transformers. Although dry transformers remove the risk of oil leaks, they are usually a lot larger in size and have larger electrical losses. These inefficiencies mean that oil immersed transformers still dominate the market.
The transformer market can also be segmented into oil types where out of mineral, silicone and bio-based oils, mineral oil (naphthenic in particular) is the most popular. This is due to its high efficiency of heat dissipation and stable chemical properties.
Regions seen to have the largest demand for transformers and their oils are countries that are modernizing their electric grids in response to rapidly increasing power demand. These include emerging economies such as India and China, which have ageing power grids and need to support growth in industrialization and urbanization.
Key market players in the power transformer industry include Bharat Heavy Electricals Ltd., CG Power and Industrial Solutions Ltd., EMCO Ltd., General Electric Company, Hitachi Ltd., Kirloskar Electric Co. Ltd., Siemens AG, and TBEA Co. Ltd.
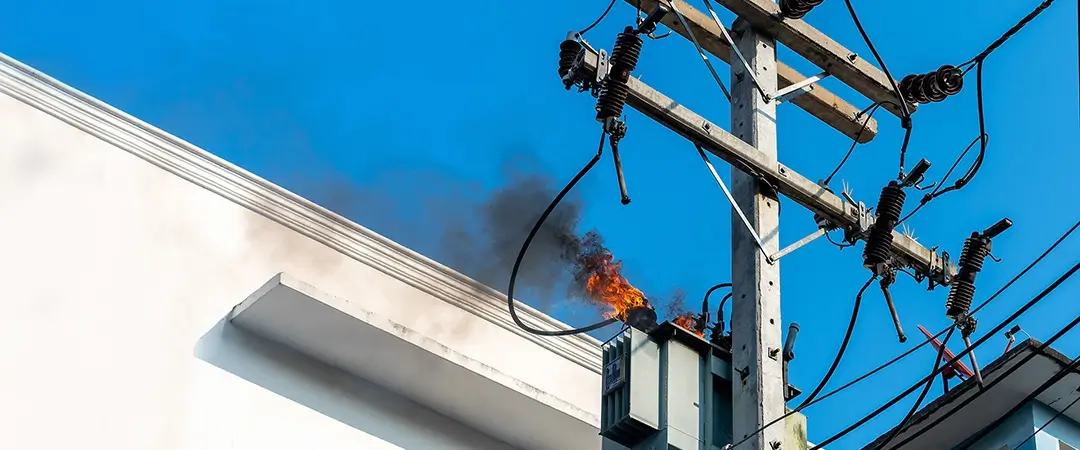
The problem: Critical equipment with many weak points
Electrical substations are responsible for stepping up voltage for efficient transmission and stepping down voltage to usable levels. In order to sufficiently dissipate heat generated from the transformer’s coils, large volumes of mineral oil that range from 500 to 30,000 gallons are necessary and are contained in 2m to 12m width containers. Typical transformers have around 10,000 gallons of oil, but this depends on the scale of the substation whether for residential or industrial power transmission. Having multiple transformers on site means there are a lot of areas to inspect.
Transformers are not the only equipment in a substation that contains oil. Circuit breakers and oil pipe cable systems that supply oil to substations add further opportunities for leaks.
Leak prone parts on a transformer
There are many parts to an electrical transformer aside from the coils and oil tank: bushings to carry the voltage to and away the transformer, radiator fins, valves, flanges and other pipework. Bushings, which are also filled with oil, are a major weak point of transformers as the end gaskets can loosen and deteriorate with time. Butterfly valves that allow oil to flow from the radiator to the main oil tank are also another critical area where even tightening the associated bolts may not prevent leaks.
Corrosion can be accelerated by environmental conditions damaging welds on the transformer and once moisture and oxygen enter, this can cause further damage. Other areas that cause leaks are where there are threaded connections for temperature probes, liquid level and flow gauges. Annual inspections of these probes if not done properly can leave connections loose and set to leak.
The true costs of small and large oil leaks
The cost of small leaks is still significant as they can cause inefficiencies in transformer performance. Exposure to the outside introduces impurities into the oil that diminish the transformer's insulating ability and increases the chance of electrical faults. Furthermore, leaks can pollute the surrounding environment via surface run-off. Just replacing the oil-saturated gravel in one substation can have a hefty cost of US$7,000.
When these small leaks are not attended to, they pose real threats of flammability. In addition, electrical faults in the transformer can produce high voltage arcing with extremely high temperatures that can vaporize oil. This leads to excessive pressure within transformers that can rupture tanks, creating serious leaks, fires, and combustion.
Considering the more serious incidents of transformers, it is clear that repairing leaks when seen at earlier stages will save a lot financially. However, costs are not just limited to the repair, as often, all oil has to be drained and replaced. Depending on the severity of damage, parts may need to be replaced and this must all be done by a specialist technician. During this time, the substation will not be operating entailing significant downtime costs.
Regular, tedious maintenance is mandatory
The danger and impact of these incidents mean that inspections are carried out on a weekly, monthly, and annual basis for high-value substations. Inspections include checking oil gauge levels, gaskets, oil quality, control switches and visual checks for cracks or leaks. Similar to repairs, these checks must be done by high-voltage technicians that are usually in charge of multiple substations. The complexity of these checks means a lot of time and money is required to confirm safe transformer operation. However, at times between manual checks, there is room for defects to go unnoticed. This is more likely to happen for lower-value substations where less frequent checks are only contracted for.
There are many potential areas and opportunities for transformers to leak, and given how critical faults can be, this calls for automatic leak detection methods over manual inspections.
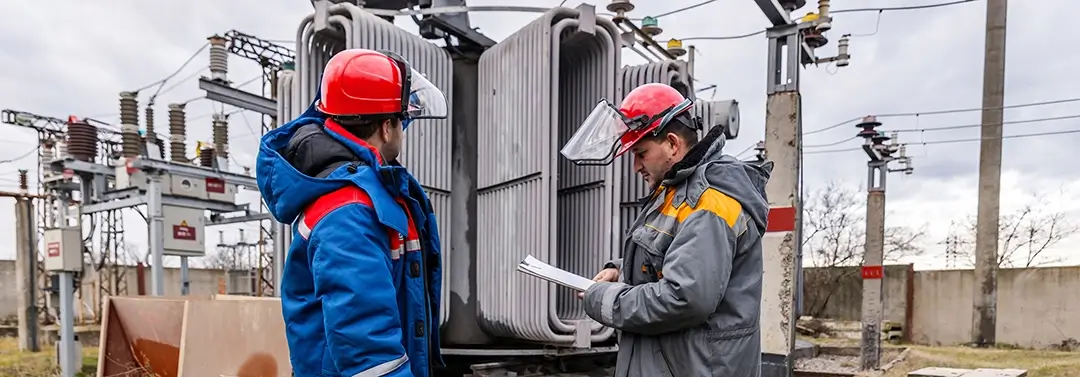
Why is the current oil leak detection market insufficient?
Current leak detection methods employed at substations are solely reactive- manual checks are done at scheduled times throughout the year. In the meantime, substations install absorbent sheets and socks to catch transformer oil to reduce pollution. Spill sheets have not changed in 40 years, which is reflected in their poor performance under sun and when wet. For larger transformers, they can be installed on top of bunds that catch leaked oils. These bunds can have liquid level gauges to measure the amount of leaked oil and notify technicians of abnormal leaks. Although level sensors can be automatic, they may not be able to detect leaks common to small cracks.
To overcome the difficulty of visual observation, oil leak paints can be sprayed onto suspected areas or a fluorescent dye can be added to the system to see leaks more clearly. These methods may be quite labor-intensive and targeted specifically to one part.
More accurate leak detection methods include acoustic and thermal imaging tests, which can reveal exactly where leaks are but because of the high-investment equipment, only suspected areas will be tested. Knowing the many weak points of transformers, this may mean areas can go unchecked.
Finally, oil sensing cables, which were originally developed for oil pipelines, can detect leaks when saturated with oil. These could be employed in substations and overcomes the reactive-nature of manual checking and has the advantage of flexible installation along any part of a transformer. Despite these benefits, sensing cables are very costly so would normally be installed sparsely, intending to detect larger spills.
It is apparent that current sensing solutions are limited to costly equipment and methods that may not be sensitive or wide covering enough to proactively notify facility managers of small oil leaks. This prevents early repairs and the time-effective use of a technician's labor.
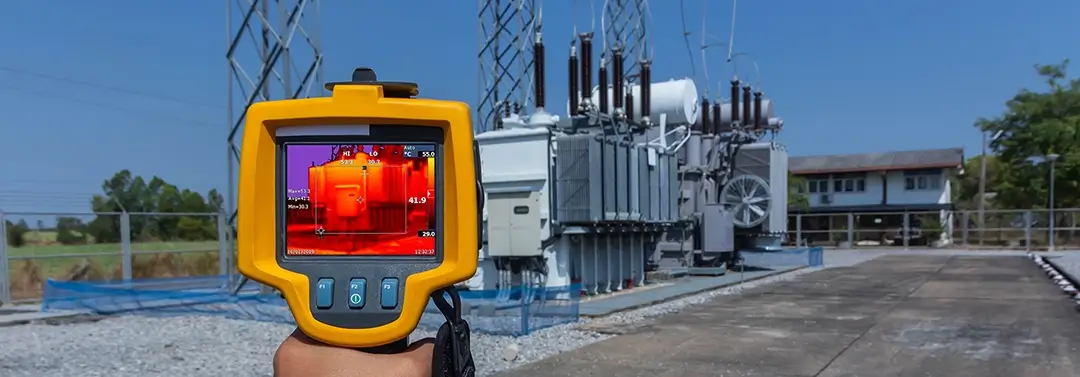
LAIIER’s solution: Unique, flexible printed capacitive sensing
At LAIIER, we champion predictive maintenance and have identified the major shortfalls the transformer market has in detecting oil leaks that can lead to detrimental consequences. We have therefore envisioned extending our current capacitive sensors to detect oil leaks. The use of printed electronics means that the sensor can be scaled to cover small or wide areas so specific components such as around transformer bushings, flanges and underneath tanks can be unobtrusively monitored. Another benefit of printed sensors is that we can easily change ink and print design to accurately detect oil presence.
LAIIER’s solution also includes being able to rapidly notify substation managers and technicians of any leaks through our LAIIER Cloud platform utilizing LoRaWAN technology. This innovative and power-efficient communication network means that battery life can span years minimizing maintenance and installation costs.
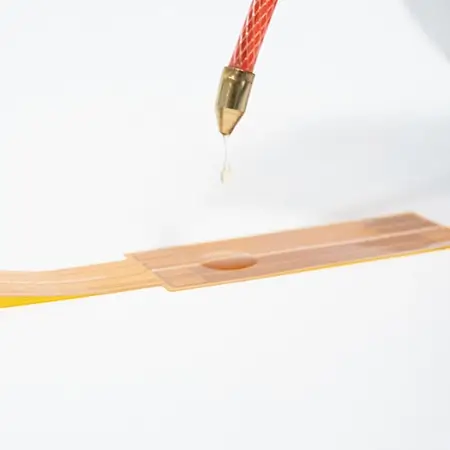
Market demand for a transformer-focused leak detection solution
Electrical grid companies
Companies that manage electrical grids, whether national or private, would want to stay one step ahead and protect their facilities from the costly impacts of oil leaks. An electrical grid company can manage hundreds of substations (for example, UK National Grid owns 330 substations) with varying amounts of transformer equipment so adopting predictive maintenance measures can make managing the whole network simpler. Also, well-serviced transformers can last up to 25 years so catching faults early with LAIIER’s leak detectors can minimize replacement costs.
Transformer repair contractors
National grid companies usually contract work out to separate transformer specialists to carry out inspection, maintenance and repairs. Transformers are complex pieces of equipment so the process of managing transformers would need thorough discussion from technical consultants and on-site engineers. This would be particularly important for transformers in large-scale industrial substations such as offshore and underground applications. Usually, checks would be done manually which could flag up issues; but with automated sensing, efforts can be targeted to address oil leaks before they escalate.
Industrial insurance firms
The numerous expenses associated with oil leaks may mean electrical grid companies would want to protect their industrial equipment with insurance. However, due to the complex technical nature of substations, policies either may not cover transformers or may only be offered at a high price. Costs have to cover contracting repairs, new parts, compensating customers and sometimes litigation from pollution or injuries obtained from transformer faults. By installing a proactive sensing system, this can reduce incidents and provide better predictability of payouts.
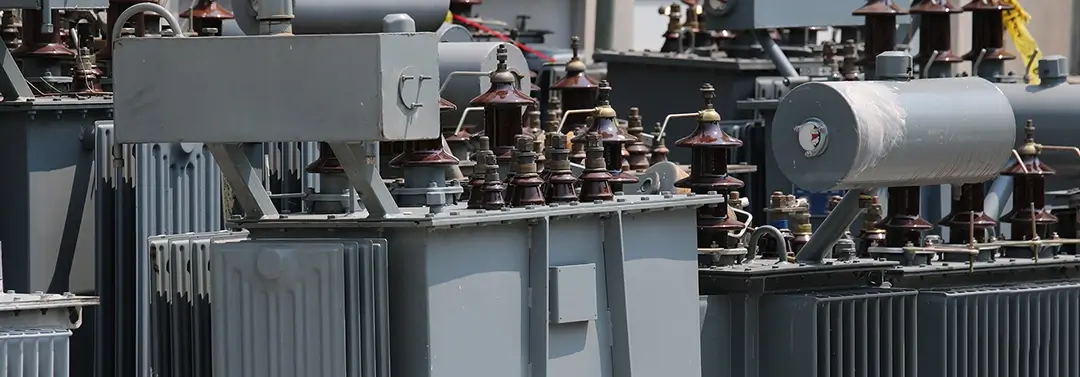
As our electrical grids expand for the world’s energy demands, transformers remain a fundamental part of this network, so rigorous and prompt maintenance is essential. The extreme electrical conditions and temperatures mean transformers have several weak points that are prone to leak oil which can reduce their performance and grow to more serious incidents. LAIIER has identified the lack of automatic sensing methods to detect the first signs of an oil leak as current methods are very manual, expensive and a risk to technicians. We have therefore proposed a sticker-like capacitive sensor that can be easily applied to transformer equipment to remotely communicate when oil leak issues have been detected. Moving a critical facility to use more predictive maintenance tools will encourage more proactive and efficient operations.