Use Case: Oil Leaks in Wind Turbines
Cleaning up the dirty side of clean energy
Early detection of oil and hydraulic fluid leaks from wind turbines.
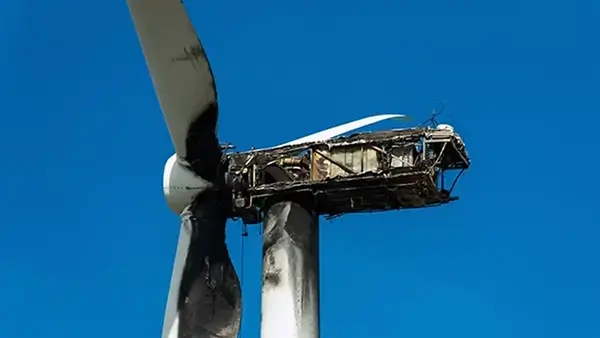
Standing higher than the Statue of Liberty at more than 300ft (100m), wind turbines are an integral part of our transition to renewable energy. Currently, there are more than 341,000 wind turbines across the globe that have the capacity to offset 1.2B tonnes of CO2 every year. With climate change an already urgent matter, world leaders have been keen to support wind energy with favorable regulations and tax credits, which is only predicted to continue.
Taking a step back, wind turbines seem simple in design: their propeller captures wind, which spins a generator to produce electricity. But in reality, there are many more calibration procedures and components to optimize energy capture in hostile conditions. The key ingredient is oil, and turbines can have as much as 1,400 liters of this inside them. Oils serve three main purposes of lubrication, hydraulics, and as gear oil - which are all essential when dealing with large torques and moving components.
The problem is that over time after constant stress, wind turbines are bound to experience damage such as cracking, pitting, and seal breakages leading to oil leaks. Despite this, servicing is infrequent as it requires scaling to the top of the turbine so leaks may be missed. Oil leaks of any kind need immediate attention as they can mean critical parts are broken. Ultimately this can lead to environmental pollution as well as turbine collapses which only put a bad name on this clean source of energy. Accurate remote detection of these oil leaks is needed to ensure faults are fixed as soon as possible.
Market opportunity for wind turbines
- The global wind turbine market was worth around US$56B in 2021 and is forecast to grow to US$102B by 2030 with a CAGR of 6.34%.
- In 2016, it was reported that there are 341,000 wind turbines globally.
- In 2022, global wind power capacity reached up to 837GW, which is equivalent to the annual carbon emissions of South America.
- In 2022, the US hads an estimated 70,800 operating turbines.
- The wind turbine lubrication market is forecast to reach US$226M by 2026.
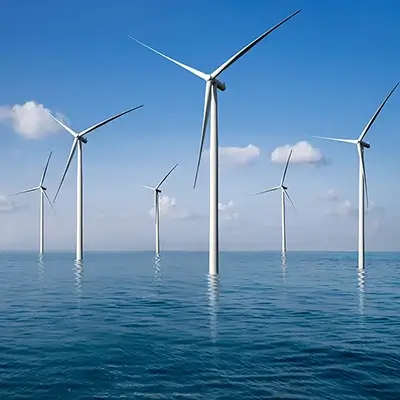
Wind power market dynamics
The global drive for wind power
Following global initiatives to address climate change like the Paris agreement, there has been an increase in sustainable energy demand. As wind power is the second largest source of renewable energy after solar, wind energy has benefitted from many favorable policy structures and regulatory frameworks. One example is the Production Tax Credit (PTC) which provides a tax credit per kilowatt hour generated for utility-scale wind farms. Frameworks like these have meant that in some cases wind generation is getting as price competitive as coal and gas plants. Furthermore, during this year’s COP27, more countries are joining an international alliance to boost offshore wind energy.
The variety of wind turbines on the market
With higher wind energy demand, this has also meant turbine technology is advancing so larger towers, blade lengths, and power ratings of up to 4 - 5MW are more widespread. Overall the wind turbine market is split into horizontal and vertical wind turbines where horizontal types are up to 10 times more efficient due to their scale - and hence are found in more remote and offshore settings.
The onshore segment dominates the global market currently with installation constituting 71.7% compared to offshore. The market can be further segmented into industrial, commercial, utility and residential scale wind farms. Utility-scale farms currently dominate the market and are defined by turbines exceeding 100kW in size that supply energy to the power grid to be distributed by utility companies.
The market is further segmented into types of drive mechanisms: gearbox, direct or hydraulic. This differentiation varies in how the spinning rotor (blade assembly) converts torque into manageable rotation speed for the generator. Although there are growing advantages of direct and hydraulic drive turbines, cost and weight have favored geared drivetrains.
Who is leading the wind turbine market?
Key market players in wind turbine manufacture, ownership, and servicing include General Electric company, Vestas Wind Systems, Nordex SE, Suzlon Energy Limited, Siemens Gamesa renewable energy, CSIC, Shanghai Electric, and Windey. One factor that wind turbine firms are becoming more conscious of are oil spills as not only do they entail repairs but also can be penalized under regulations like the EPA’s Clean Water Act. Additionally, international oil company ExxonMobil, is stressing the need for ‘real-time condition monitoring’ for use in remote turbines as this will lead to an ‘extended service interval and a lower environmental footprint’.
Geographically, China and the US account for over half the world's wind power capacity and in 2020, accounted for almost 75% of new wind turbine installations. The Asia Pacific region is predicted to continue growing and dominating the market where China, Japan, and India remain the largest markets. Other notable countries include Brazil, Mexico, Vietnam, and Australia. Wind power demand is also growing rapidly in the EU, where electricity generation from wind grew from 3.9% to 12% between 2008 and 2019 .
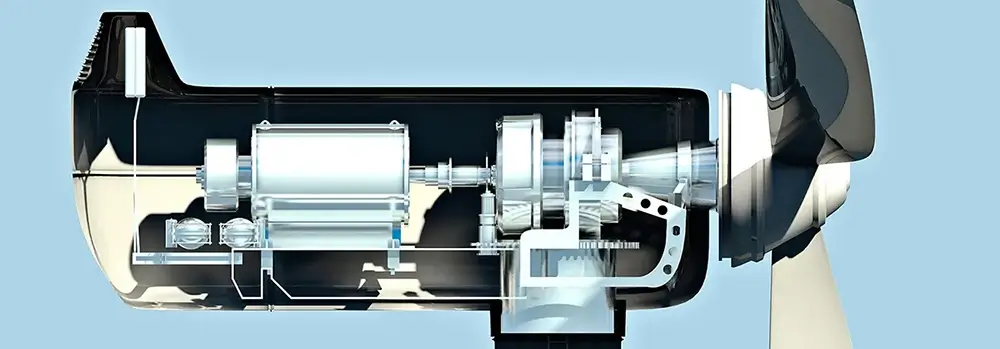
Why do wind turbines need oil and hydraulic fluid?
Before we get into the problems of turbine oil leaks, it is important to locate the multiple areas of a turbine that contain oil whether in the form of lubrication, hydraulic fluid, or gear oil.
Gearboxes
The drivetrain mechanism is most commonly a gearbox. The gears connect the low-speed rotating rotor and increase rotational speeds from around 50rpm to up to 1,800rpm. This major jump requires a huge assembly of industrial gears that depend on gear oil to ensure smooth rotations and to keep temperature stable. As this oil is critical to the gearbox’s function, there are normally separate compartments for the gearbox cooling system and the oil filtering system to remove any impurities.
Yaw and pitch drives
To optimize performance, wind turbines can rotate in two ways to improve wind capture. First, the yaw drive keeps the wind turbine head (nacelle) pointed to the wind. Next, the pitch drive rotates all the blades to the right angle. Both can be tuned to either maximize wind capture or minimize it if wind conditions become too harsh. These drives are either powered by electromechanical means (gears) or using hydraulics where the latter is more reliable and cost-effective. Therefore these components depend on a network of hydraulic fluid to operate.
Lubricants
Additionally, lubricants are also essential in wind turbines for any part that moves. This includes bearings on the spinning rotor, main shaft, generator and the drivetrains for yaw and pitch control. The wide range of components that need greasing translates to a variety of lubricants specialized to its purpose: rust and oxidation inhibited, anti-scuff, or compounded gear lubricants.
Brakes
Wind turbines all have a stop mechanism to brake rotor speed in emergencies or when components get too hot. This disc brake is usually implemented by hydraulic means or mechanically so plenty more hydraulic fluid or gear oil is required.
Transformers
Lastly, a forgotten part of the turbine that contains significant amounts of oil is the built-in step-up transformer that processes the produced power from the generator. To read more about the dangers of transformer leaks, LAIIER has already explored this in a separate use case.
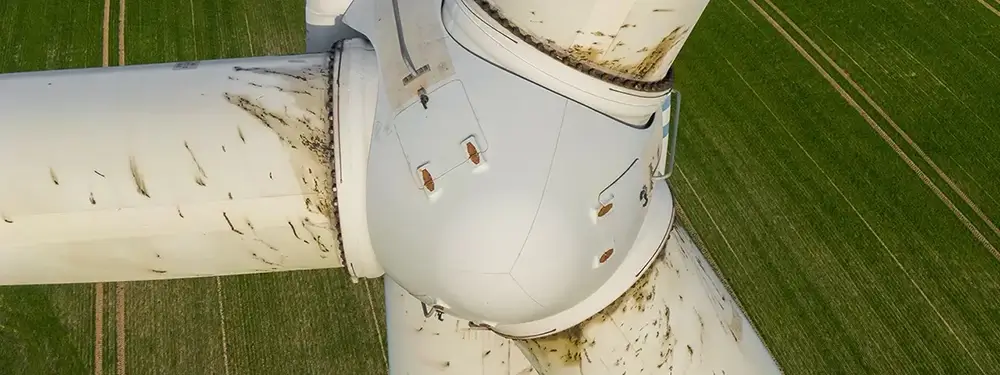
The problem: Damage-prone turbines that are difficult to service
Harsh winds, vibrations, and torques
Turbines, as a vessel for up to 1,400 liters of oil, hydraulic fluid, and lubricants, have many opportunities to leak. Generally, turbines can last for longer than 20 years but must be serviced regularly because of the extreme environments they operate in. Wind turbines stand at around 100m in altitude so can experience extreme winds reaching up to 200mph (exceeding their maximum operating speed of 65mph) in hurricane conditions, so must be able to withstand these forces and vibrations. On top of these strong winds, they are also subject to rain, fog and salt water which are all factors that accelerate corrosion.
Under average environmental conditions, gears and shafts can experience torque of around 2.5M Nm. Varying torques can create repeated strains and stresses to the equipment which over time can lead to cracks and defects. This is why every wind turbine has a smart controller to adjust turbine orientation or even brake the wind turbine.
Oil and hydraulic fluid deterioration leads to critical failures
Even under smart control, lubrication and gear oil can be unpredictable as film strengths vary under changing pressures and temperatures. This is highlighted by how gearboxes are one of the leading sources of wind turbine failure. Other areas that cause oil leakages include deteriorating seal rings, blocked oil filters, and if oil pressure is too high, pipe ruptures can occur.
Another problem that occurs inevitably is the contamination of gear oil and/ or lubrication, which increases in dustier conditions. Dust will mix into tight spaces (like bearings) and acts as an abrasive, wearing away critical components via micropitting. Turbines have oil filtering or servicing to make sure there is minimal disruption but in some cases, pitting can gradually lead to oil leaks and catastrophic failures.
As soon as turbines start to leak oil, this is an immediate trigger to much more serious issues. When oil levels in gearboxes drop below a certain level, this can jam gears, causing cracks that in the worst-case scenario can destroy a whole turbine. This can be similarly linked to the hydraulic systems in that if it is not sufficient to rotate the turbine, it can fail to protect it from strong winds.
Servicing is very difficult
Wind turbines require regular maintenance but this is made harder by their remoteness and scale. Specialized engineers must be able to get to the top of each 100m turbine, which is considerably harder offshore. Also if parts need replacing, industrial cranes need to be brought to site, which is extremely cost-intensive. Repairing or servicing may even be impossible if wind conditions are too dangerous.
Because maintenance is difficult, wind turbine design strives to ensure all parts are self-sufficient. This allows them to be serviced once every 6 to 12 months. Also as turbine lubricants and gear oils are becoming more advanced, lubrication intervals are getting further and further apart: now state-of-the-art gear oil can last up to 10 years. This encourages less frequent gear oil changes and other servicing requirements but can also lead to faults being unattended to for longer periods.
The indirect but costly impacts of wind turbine oil leaks
If oil leaks happen, they can cause a lot of environmental damage. Oil can contaminate farmlands and forests, and becomes particularly problematic when it spreads into groundwater or worse into the sea from offshore turbines. Once these chemicals enter water sources, they are hard to track and can spiral into other social, health and livestock issues.
As well as the detrimental impacts on the environment, the cost of a wind turbine's downtime is economically significant. Gearboxes are the most likely source of issues and an average 2MW turbine gearbox costs from US$2-4M. Furthermore, in the case of a Swedish wind farm, one collapsed turbine meant the other 104 other turbines had to be halted. It is estimated that the downtime costs just for energy generation was over US$7M per week.
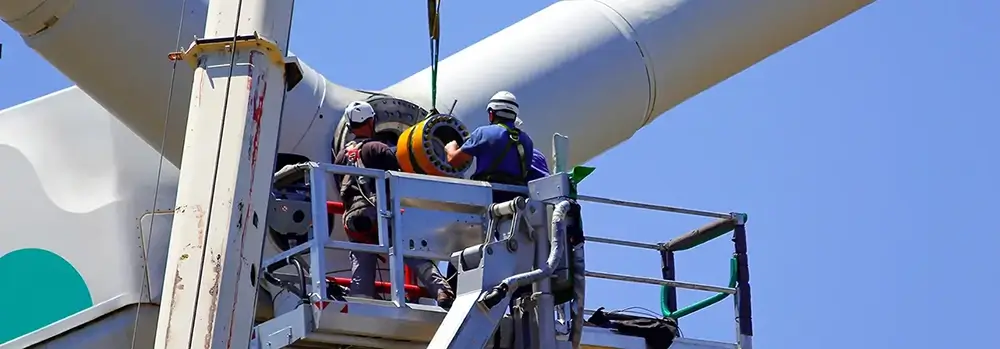
Why is the current oil leak detection market insufficient?
Considering these impacts, there must be a way to avoid oil and hydraulic leaks that lead to costly failures. As mentioned servicing can happen to sample oil to check for chemical abnormalities but this depends on technicians to access the infrastructure. On newer wind turbines, remote oil quality sensors have been employed to automatically monitor properties such as oil viscosity, acidity, oxidation and additives. Other sensors found on wind turbines are temperature, vibration, and pressure sensors. Whilst these methods can detect changes in oil quality and the physical integrity of the turbine, oil leaks can still go undetected.
Oil level monitoring is also common within wind turbines where sumps or trays around critical components can detect the amount of oil leaked. However, these level monitoring systems may not be sensitive enough to notice the first trickles of oil. Spotting the start of an oil leak is the key clue to further damage.
Looking at existing oil leak sensors for contexts outside of wind turbines, these still are very manual processes that need in-person access to a turbine nacelle. These include oil leak paints, and acoustic and thermal imaging.
An automatic remote solution designed by Sensative uses slim sensors that can be mounted to likely-to-leak areas. This directly detects leaks however have limited detection space so oil leaks may have to spread significantly before being detected. To overcome this, oil sensing cables could be another solution in wind turbines as they have the advantage of flexible installation along any part of a turbine. Despite these benefits, sensing cables are very costly so would normally be installed sparsely, intending to detect larger spills.
It is clear that there is still a need for a remote, easy-to-install, wide-covering sensor to reliably detect the first drops of an oil leak.
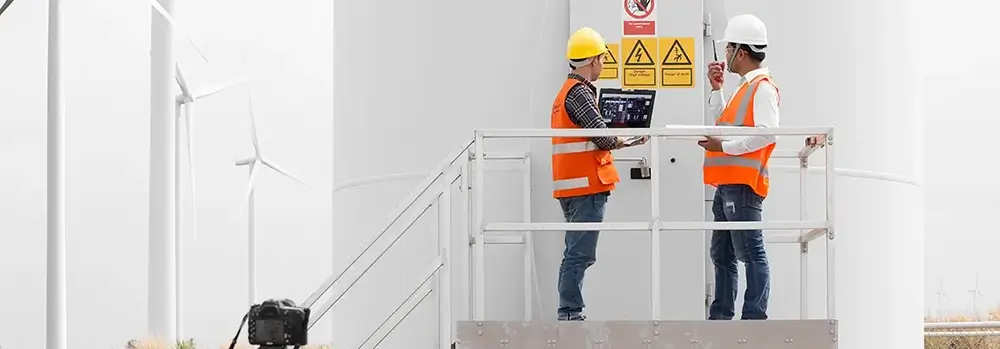
LAIIER’s solution: Unique flexible printed capacitive sensing
At LAIIER, we champion predictive maintenance and have identified the major shortfalls the wind turbine market has in detecting oil leaks that can lead to detrimental consequences. We have therefore envisioned extending our current capacitive sensors to detect oil leaks. The use of printed electronics means that the sensor can be scaled to cover small or wide areas so specific components such as around rotor bearings, tower flanges and gear boxes can be unobtrusively monitored. Another benefit of printed sensors is that we can easily change ink and print design to accurately detect oil and hydraulic fluid presence.
LAIIER’s solution also includes being able to rapidly notify wind farm service providers and technicians of any leaks through our LAIIER Cloud platform utilizing LoRaWAN® technology. This innovative and power-efficient communication network means that battery life can span years minimizing maintenance and installation costs. LoRaWAN is also great for sending messages over large distances of more than 15km - perfect for offshore and remote wind farms.
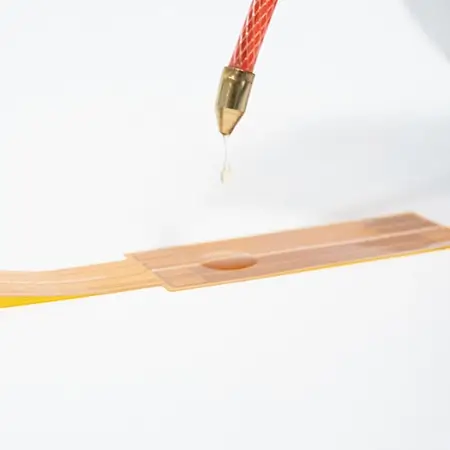
Market demand for a wind power solution
Wind farm service providers and operators
Wind farm owners usually sign service agreements for their wind turbines to ensure their infrastructure is under warranty whilst being serviced regularly. Service providers are responsible for diagnosing wind turbines of any apparent issues and predicting possible expenses throughout the turbines’ life. This is a large task and can become especially complex in that one service provider can be in charge of up to 13,000 wind turbines. The sheer amount of turbines with the potential costs of failures would extremely benefit from remote, accurate sensors.
Wind turbine maintenance technicians
Service providers usually hire third-party contractors to tend to potential wind turbine faults. As these technicians go to great lengths to access the head of the turbine, it only makes sense that they have a full understanding of the issues and dangers. This will increase the efficiency of resolving broken components whilst reducing costs. For example, wind farms very rarely hire industrial-scale cranes to fix turbines because of their cost, but if they know there is a cluster of faulty turbines, this makes equipment hire a lot more economical.
Insurers of wind farms
Managing and creating policies for wind farms requires a rigorous technical capability to understand the unpredictable nature of weather conditions and high-investment components of a wind turbine. This coupled with the many stakeholders involved in a wind farm’s operation means that it can be difficult for insurers to know how to plan well-informed policies for wind farm owners. Remote oil leak sensing devices tuned to detect the start of issues would give data-backed insights to better inform their decision-making and ultimately save large payouts.
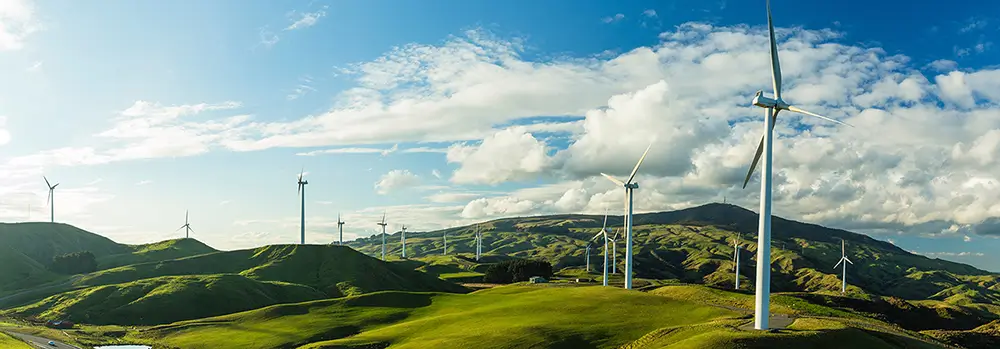
As the world strives for more renewable energy, the demand for wind farms will only grow. Their trajectory to achieving reliable energy production, however, depends on whether wind turbines can adopt the use of smart sensors to predict when maintenance is required. As we have identified in this use case, oil leaks are a serious tell-tale sign of internal issues as well as the potential for environmental and economic harm. Service operators must therefore act quickly to repair necessary areas, but the fact that site inspections only happen one or two times a year may mean oil leaks can be left to escalate. LAIIER has recognized this dire opportunity by proposing the use of capacitive sensing stickers to detect the first signs of an oil leak. This will transform wind turbines to take a more proactive approach to fault finding, taking away the risk to technicians and promoting more efficient operations.